Three steps to take to maintain your samplers
Our cars wouldn’t run very well if we didn’t fill them with gasoline, change the motor oil, or conduct routine maintenance and repairs. In the same way, your facility’s sampling equipment needs regular preventative maintenance.
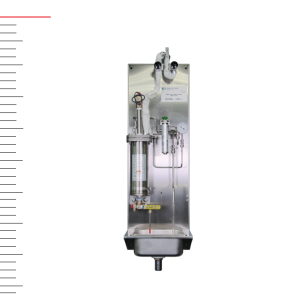
Proactive and regular maintenance on your sampler is one of the best ways to maintain its peak performance and avoid malfunctions or breakdowns during use – which can lead to significant losses in plant productivity and efficiency. Preventative maintenance involves the following three steps:
1. Detailed inspection for visual signs of wear, leaks, abrasion or chemical attack of components and seals. Ask: Is the sampler in good working order? Is maintenance during planned outages sufficient to keep it running well? Is the sampler on a regular maintenance schedule? Would failure present safety concerns, significant unplanned downtime or risks to other plant assets?
2. Monitoring the progression of these visual cues to evaluate how well the sampler is performing within your process. Ask: Does it need any maintenance at this time? Will a one-time repair restore the efficiency of the sampler? If so, when can it be done with little or no disruption to the process? Should parts be stocked on site?
3. Evaluating usage so you know how often sampling is conducted, how long the sampler has been in operation before wear or between scheduled maintenance times, and its expected lifecycle. Ask: Is the sampler at the end of its lifecycle? How can replacement be managed to minimize downtime?
- Regularly scheduled maintenance should minimally include:
- Properly cleaning the sampler of any process material, and lubricating its components
- Calibrating the sampler so it continues to run at optimal capacity
- Replacing worn components to keep it operating safely and at peak performance
Keeping an on-site inventory of stock parts like seals and gaskets that regularly show wear, so they can be replaced as needed with no unscheduled downtime
To provide long-term value, Sentry® sampling solutions are designed for long wear, and when repair is needed due to poor maintenance, our equipment can be rebuilt when a full replacement is not an option. If you find your samplers are not working optimally, we offer complete refurbishment service right at our factory for worn or damaged Sentry equipment. We offer:
- Complete equipment disassembly and inspection
- Service repairs made by our professional, factory-trained experts
- Factory certification and testing of your samplers
- Coverage by our standard warranty for any parts installed and work performed on your sampler
Each sampler rebuild follows an ISO-approved process, beginning with a thorough inspection of every component and ending with rigorous testing to ensure quality and performance.
This article was written by Paul Williams and first appeared in The Monitor, Sentry-Equipment.com.