Using Steam to Improve Plant Performance
Optimal performance has varying meanings across the plant. For some, cost takes precedence, and for others, system uptime or product quality is the critical priority. Maintaining this balance while meeting ever-changing regulations demands a multi-skilled approach and professional support. Your business requires a partner who understands the unique challenges you face. GESTRA understand these challenges and can offer the support you need such as product advice, process evaluation, or system design consultation.
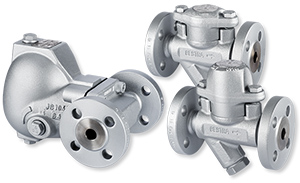
Your processes rely on a consistent supply of steam at the correct pressure and temperature. While the boilerhouse does need to run cost-effectively, and efficiently. For most steam systems, that means managing the effective removal of condensate.
In the first instance, the steam trap population is the first opportunity for improving plant performance. Failing steam traps not only mean increased energy costs, but also impact upon consistent temperatures for process fluid control, affecting product quality, and causing productivity issues.
To keep your plant running at peak performance, system uptime needs to be maximized. For many plant managers, that can mean proactive maintenance or having engineers ready to help. By avoiding unscheduled maintenance and downtimes, plant performance remains at optimal levels.
A busy plant still needs to meet safety and regulatory rules. As we enter an increasingly globalized world and make further technological advances, regulations are subject to change. Each element of plant performance is dependent on the other to create an optimum environment. Production, costs, and saving energy all need to be delivered in a safe environment.
This content originally appeared on Gestra.com.
Explore the GESTRA products available through Benchmark Instrumentation and Analytical Services.